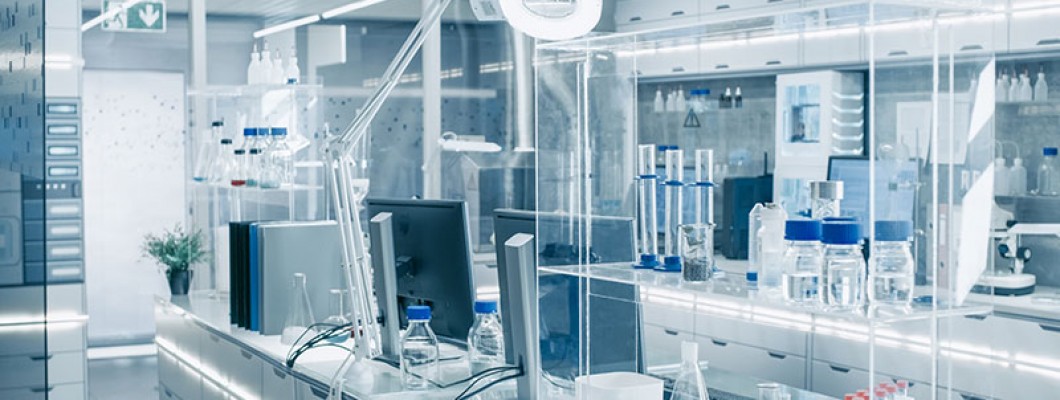
Laboratory equipment management refers to the systematic and organized approach to acquiring, maintaining, calibrating, and ensuring the proper usage of equipment in a laboratory setting. It involves a series of processes and practices aimed at maximizing the efficiency, safety, and longevity of laboratory instruments and devices. Here are some key aspects of laboratory equipment management:
Acquisition and Procurement: This involves selecting and purchasing the appropriate equipment based on the laboratory's needs, budget, and research objectives. It includes evaluating specifications, vendor options, and warranties.
Inventory and Asset Tracking: Laboratories maintain a detailed inventory of all equipment, including their make, model, serial numbers, acquisition dates, and maintenance records. This helps in tracking the location and condition of equipment.
Calibration and Maintenance: Regular calibration and maintenance schedules are established for equipment to ensure their accuracy, precision, and reliability. Routine checks, servicing, and adjustments are performed to keep instruments in optimal working condition.
Training and User Manuals: Proper training is provided to laboratory personnel on how to operate, maintain, and troubleshoot equipment. User manuals and documentation are made readily available for reference.
Safety Compliance: Equipment management includes ensuring that all safety protocols and guidelines are followed during equipment use. This includes maintaining safety features, such as emergency shutdowns and safety interlocks.
Repair and Replacement: When equipment becomes faulty or outdated, a process for repair or replacement is initiated. Decisions are made based on factors like the cost of repair, availability of spare parts, and technological advancements.
Record Keeping: Detailed records are maintained for each piece of equipment, documenting maintenance history, repairs, and any incidents or issues that may have occurred during use.
Asset Retirement: When equipment reaches the end of its useful life, a proper disposal or retirement process is followed, which may involve safe disposal, recycling, or resale of the equipment.
Budget Management: Laboratories allocate budgets for the acquisition, maintenance, and replacement of equipment. Effective budgeting ensures that resources are efficiently utilized.
Regulatory Compliance: Laboratories must adhere to regulatory requirements and standards governing the use and maintenance of specific equipment, especially in fields such as healthcare, environmental testing, and pharmaceuticals.
Risk Assessment: Assessments are conducted to identify potential risks associated with equipment use and to develop strategies to mitigate those risks.
Documentation and Audit Trails: Detailed documentation is crucial for audits and inspections. Records should be readily accessible for compliance checks.
Effective laboratory equipment management ensures that the laboratory functions smoothly, maintains the quality and reliability of research results, minimizes downtime, and promotes safety. It also helps laboratories make informed decisions about equipment upgrades and replacements, ultimately contributing to the success of research and experimentation.